After stop working for two mounth due to other important projects I am back now. Where should I start after such a long time? I decided to improve something I thought it is already finished: the engine mount [

)]
The modification are four bolts connecting the upper and lower braces.
This courses holes in the frame
These are not only holes but I welded tubes inside so the bolts cannot deform the main tubes. Sorry for the bad picture, I didn't manage to connect this low-cost endoscope to my computer. What you can see are tubes not the bolts.
I hope that this sub project is really finished now.
And if you lost the overview about the different stages of engine mount, here is a picture of the engine mount cemetery.
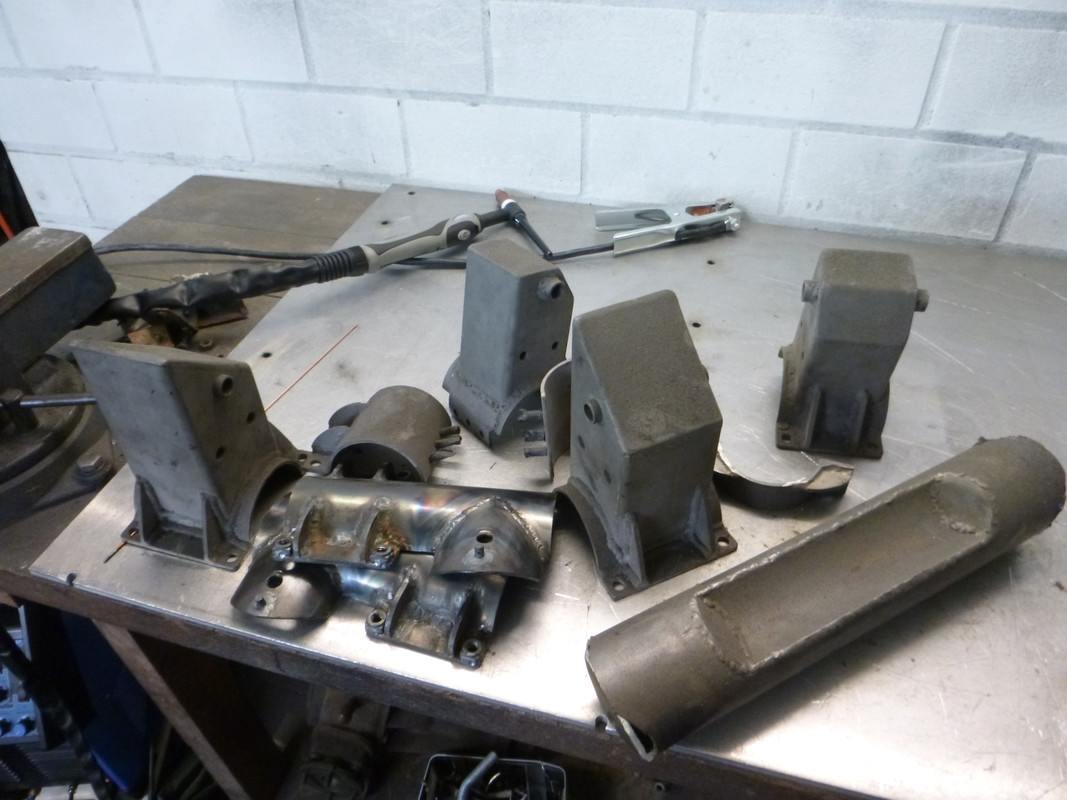